La culture de l’amélioration continue et de la performance sont au cœur du lean. Parmi les outils qui sont au service de cette méthodologie sûre, on retrouve le système andon. Ce dispositif, permet de signaler une anomalie dans le processus de production.
Pour en comprendre son objectif et ses avantages, il est cependant nécessaire de revenir sur le fonctionnement de cette méthode. IBITEK éditeur du logiciel de suivi et pilotage de production en temps réel IBIProd vous explique ce qu’il faut savoir sur ce système et l’industrie connectée.
Qu’est-ce que le système andon ?
Définition
Système de gestion visuelle utilisé par les gestionnaires et les opérateurs dans l’industrie manufacturière, la méthode andon permet de déterminer et d’afficher facilement l’état des lignes de production.
L’optimisation de la production industrielle avec l’andon lean
L’optimisation de la production industrielle est un concept complexe qui nécessite une évaluation minutieuse et une expérience pratique pour être correctement mis en œuvre. De nombreuses variables doivent être prises en compte, notamment le processus actuel de fabrication, l’équipement utilisé et sa configuration par rapport aux autres machines.
Aujourd’hui, cette méthode est utilisée dans l’industrie lourde, l’industrie à processus continu et industrie des matériaux.
La méthode qualité
En cas de difficultés ou d’anomalies rencontrées sur leur chaîne de production, les opérateurs se manifestaient par un signal lumineux, à savoir une lanterne de papier (ou « andon »).
Très rapidement, ce système s’est imposé avec un panneau lumineux qui permet de mettre en évidence une faille dans la production.
Lorsque ce signal est activé, les opérateurs qualifiés ou chefs d’équipe (team leaders) arrivaient sur la chaîne de production pour résoudre le problème.
Ils réfléchissaient également aux causes et aux moyens de résoudre les cas d’anomalies sur le long terme.
Quels sont les avantages de la méthode andon pour l’industrie connectée ?
Cette méthode présente de multiples avantages pour l’industrie connectée :
- Une réduction des coûts : la réduction du temps perdu aide à diminuer les coûts de gestion de production induits par les arrêts non planifiés.
- Un gain de temps non négligeable : grâce à l’affichage visuel des problèmes, le site industriel évite les gaspillages liés à la recherche d’informations ou de pannes causées par l’arrêt de la chaîne de production.
- Une meilleure communication intrinsèque : l’affichage visuel et sonore favorise également un meilleur flux de communication interne entre les différents intervenants du processus de production.
- La remontée de l’information : avec le système de management visuel issu de la méthode andon, les informations remontent avec efficacité depuis les plus bas niveaux de la hiérarchie de l’organisation jusqu’aux postes décisionnels. Les opérateurs peuvent ainsi avoir une meilleure visibilité et une bonne compréhension du fonctionnement de la chaîne de production.
- Un meilleur contrôle : en anticipant les problèmes, la méthode permet à la direction et aux équipes de maintenance d’avoir plus de contrôle sur la chaîne de production.
Elle favorise également la consolidation des données essentielles à la performance de l’entreprise, car le système enregistre les anomalies, leur régularité et permet de partager l’information avec des tiers qui n’ont pas subi directement le problème.
Le lean management : ses objectifs pour une industrie connectée
Le lean management désigne l’ensemble des techniques qui visent à éliminer toutes les activités à faible valeur ajoutée. Le terme « lean » veut dire en français « moindre ».
De ce fait, le lean management est une technique de gestion essentiellement concentrée sur la réduction des pertes générées à l’intérieur d’une industrie connectée, pour un rendement et une production plus justes.
Cette méthode de management a plusieurs objectifs tels que la diminution des stocks, la gestion du gaspillage, la limite des coûts superflus, la réduction de la durée des cycles de production ou encore l’augmentation de la productivité. Le lean management a également pour objectif d’optimiser la qualité.
Cette méthodologie favorise aussi l’implication de tous les salariés et permet d’améliorer la performance globale de l’entreprise.
Pour être efficace, la méthode du lean management doit être mise en œuvre à tous les niveaux de l’industrie et inciter la bonne communication entre les différents services ainsi qu’entre les unités de production.
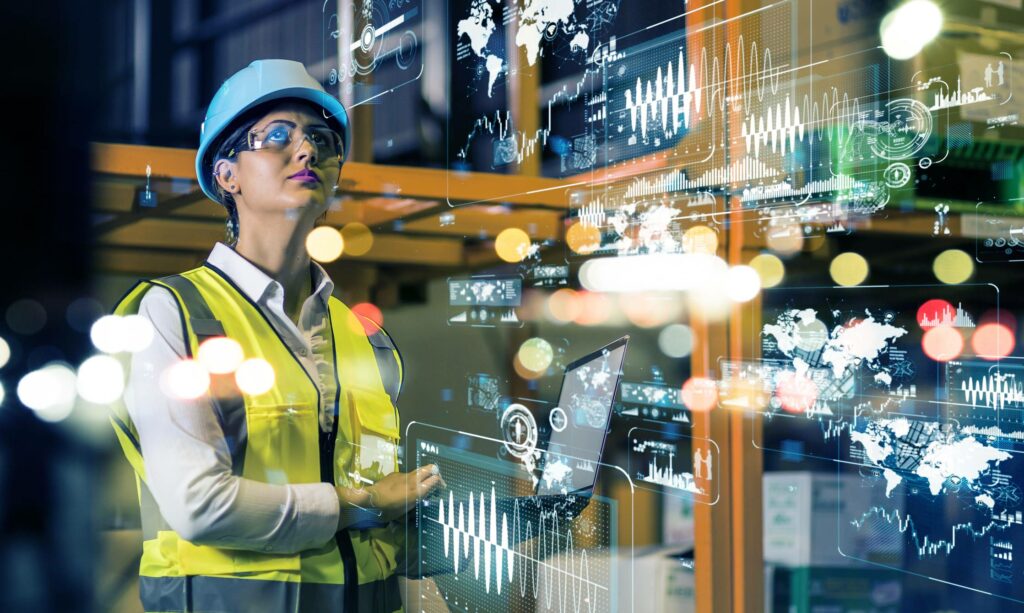
Découvrir les différents outils du lean management
La palette des outils du lean management est assez large et généralement décrite comme un ensemble de solutions d’expérimentation et d’apprentissage.
Le personnel de l’entreprise se les approprie et collabore dans une démarche d’amélioration continue.
En résumé, il existe de nombreux outils du lean management notamment:
La méthode 5S (débarrasser, nettoyer, ranger, ordonner et être rigoureux)
Cette technique permet d’optimiser l’environnement de travail et de réduire les gaspillages de temps.
Le management visuel
Ce type de management permet de partager l’information et de résoudre les différents problèmes.
La méthode Six Sigma
Cette méthode a pour objectif d’améliorer l’efficacité et la qualité des processus.
La méthode Kaizen
Cette méthode permet de perfectionner de façon continue les processus.
La méthode Value Stream Mapping (VSM)
Cette méthode vise à analyser les processus et à identifier les freins.
La méthode Kanban
Cette technique se concentre sur l’optimisation de la gestion des stocks.
La méthode SMED
Cette méthode vise à diminuer le temps de changement de série.
Bien qu’il soit à l’origine apparu au sein de l’industrie automobile, le lean management peut être déployé partout, quel que soit le secteur ou la taille de l’entreprise.
Quels sont les avantages du lean management pour l’industrie connectée ?
La mise en place des méthodes du lean management permet aux managers de bénéficier de nombreux avantages, notamment l’amélioration de la productivité et de l’efficacité des employés.
En effet, les employés qui se consacrent à la création de valeur ont la possibilité d’augmenter leur efficacité et leur productivité, car ils seront plus concentrés sur les tâches importantes et à forte valeur ajoutée.
Très utile dans l’industrie connectée, le lean management est aussi un système plus intelligent.
En établissant un système de traction, les employés sont en mesure de fournir du travail uniquement lorsqu’il y a une demande réelle.
Cette méthode permet également une meilleure utilisation des ressources, en se basant sur une production qui est fonction de la demande réelle, avec des employés qui ne peuvent utiliser que les ressources nécessaires, ce qui permet d’éviter les gaspillages.
Par conséquent, le personnel se concentrera davantage sur les activités qui apportent une vraie valeur à l’entreprise.
L’entreprise devient ainsi plus flexible et capable de répondre efficacement et rapidement aux exigences des consommateurs.
Qu’est-ce que le lean manufacturing ?
Le lean manufacturing désigne une stratégie d’entreprise qui offre la possibilité de délivrer des services et des produits qui correspondent aux attentes des clients, dans la quantité requise, au moment souhaité et au juste prix.
Pour réaliser une production lean, un minimum d’équipements, de matières, de main-d’œuvre, d’espace et de temps est utilisé.
Basé sur l’élimination des gaspillages au sein des processus de production, le lean manufacturing est une méthode d’organisation d’optimisation de la performance industrielle qui vise à respecter les exigences du client.
En d’autres termes, il s’agit d’analyser de manière détaillée les différentes étapes du processus de production, puis d’éliminer tous les gaspillages identifiés tout au long du processus de fabrication.
Parmi ces sources de gaspillages, on retrouve la surproduction, l’excès de stock, les stocks inutiles, les temps d’attente, les démarches et les déplacements inutiles, les transferts inutiles, de même que les erreurs, les défauts et les rebuts.
Indispensable pour le bon fonctionnement d’une industrie connectée, le lean manufacturing repose essentiellement sur l’objectif des 5 zéros, c’est-à-dire zéro stock, zéro délai, zéro papier, zéro panne et zéro défaut.